Five Ways to Outsource your Hardware Product Development
Discover five outsourcing options for tech consumer/commercial product companies. The post is based on my experience working with overseas contract manufacturers, JDMs, ODMs and OEMs.
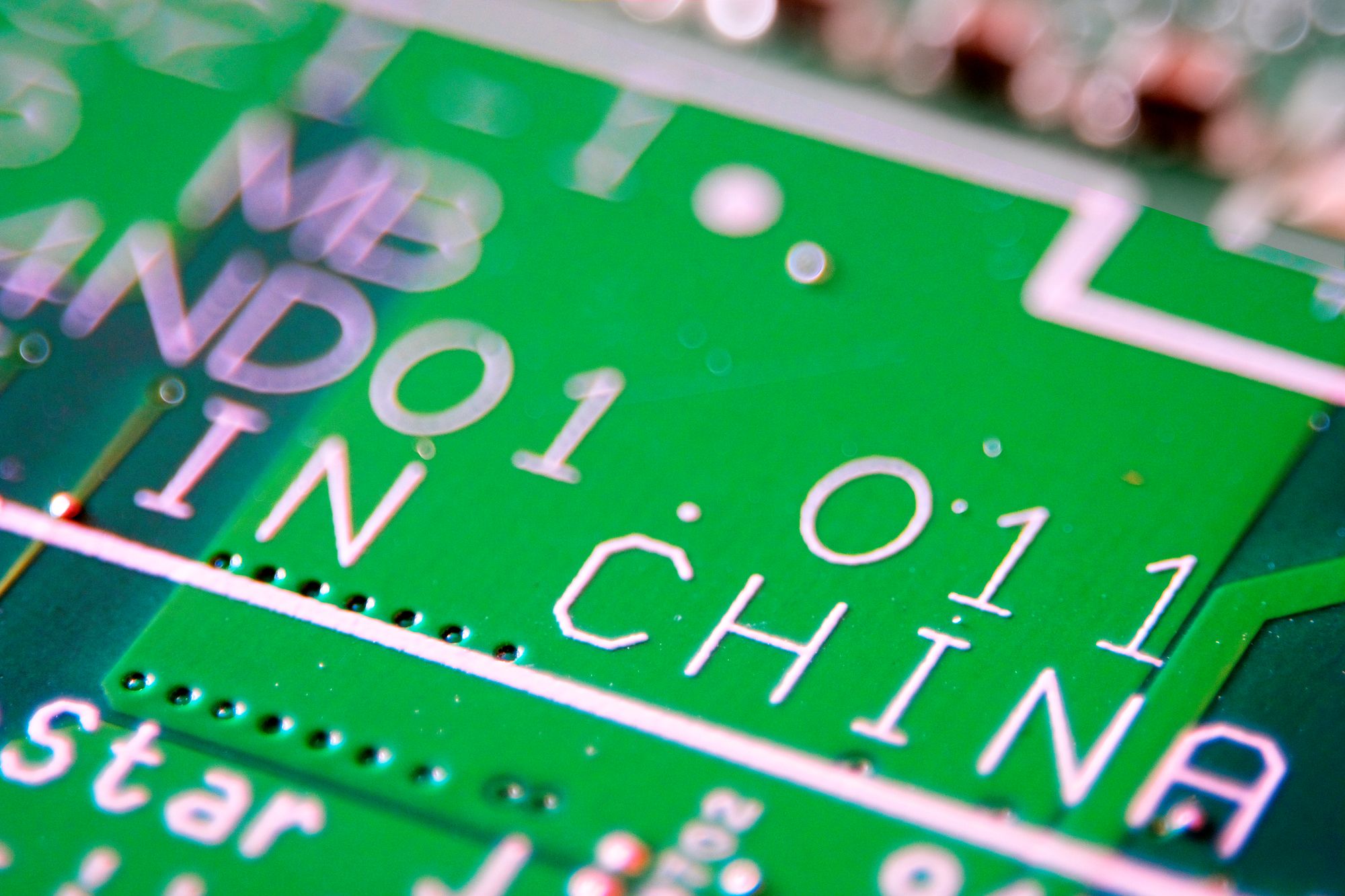
Outsourcing involves the contracting out of a business process to another party. There are many reasons to outsource, among which lower operational and labor costs, delegate non-core practices, leverage expertise not available in-house, expand the workforce to cope with a resource crunch and the list goes on. Outsourcing is a very common practice in the technology industry, in particular for mass market consumer hardware products. Most often than not, outsourcing is associated with manufacturing and assembling of products in Asia, but there is actually a full spectrum of possible scenarios that I want to highlight in this post.

I have had experience with most of them, and I realize the terminology can sometimes be confusing. The table above summarizes five of the possible outsourcing scenarios that I have come across. For simplicity the table assumes a project as composed by four basic steps: first the specifications are defined based on the application and business goals of the product (SPEC). Then the device is designed (DESIGN), manufactured (MFG) and finally assembled (ASSY) into a final product.
EMS (Electronic Manufacturing Service) and CMS (Contract Manufacturing Service) are the most common type of outsourcing. In these scenarios, the design is done in-house while the manufacturing of submodules (e.g. electronic boards) and assembly is outsourced.
In the Joint Development Manufacturing (JDM) model, the outsourcer and the outsourcee work together on the design and manufacture of the product. I have seen this model be used for high volume and complex innovative hardware projects, where the design and manufacturing present challenges and the final product is expected to ship in the hundred of thousands (or more) of units.
An ODM, or Original Design Manufacturing, is a company that designs a product based on a client's specification. This model is heavily used for common consumer products. Take notebooks as an example: big brand names, such as HP and Dell, come up with the specifications of their next device, but it is then companies such as Wistron, Pegatron, Inventec, Quanta, Compal and Foxconn that will eventually design, manufacture and assemble it. The outsourcer can influence the design to a certain degree, but that comes fat an extra price, as I soon learnt in my career when I tried to influence an ODM to use one IC instead of another in their solution...
Finally OEMs, or Original Equipment Manufacturing, are companies that do it all, from spec definition to assembly. Usually an OEM makes parts or subsystems that are meant to be integrated into another company’s end product. If you have ever tried to assemble a desktop computer yourself you have probably stumbled across several OEM parts, such as DVD units, video cards etc.
These are the main outsourcing paradigms that I have encountered. The reality is much more fragmented and the lines between different scenarios are quite blurred and allow all sorts of collaborations between tech companies and Asian high tech contractors.